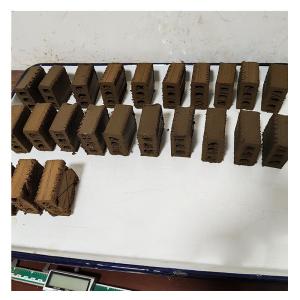
Add to Cart
BRICTEC Brick Raw Material Analysis Service for Composition Analysing and Testing
Xi'an Brictec Engineering Co., Ltd. provides a series of brick factory services including: raw material analysis, design and guidance, accessories supply, upgrade and improvement, production management, etc.. Among them, raw material analysis helps to understand clients' raw material conditions clearly, providing clients with more professional and accurate brick making solutions.
Raw material analysis includes 7 parts:
1. Raw material physical properties
2. Raw material chemical properties
3. Drying properties
4. Firing properties
5. Lime bursting test
6. Frosting test
7. Conclusion and suggestion
Sample Display
1. Raw material physical properties
Report number: | ||||||||
Raw material | clay | Raw material source | ||||||
Entrusted party | Submit date | 8-Oct-23 | ||||||
Submit party | Analysis | physical property | ||||||
Analysis result | ||||||||
Analysis item | Platts shaping moisture(%) | Plasticity | Critical moisture content | Drying sensitivity coefficient | Drying line shrinkage rate(%) | |||
(%) | ||||||||
Raw material | Liquid limit | Plastic limit | Plasticity index | |||||
(%) | (%) | |||||||
clay | 17.87(dry basis) | 23.43 | 17.75 | 5.68 | 11.13 | 0.59 | 1.76 | |
15.16(wet basis) | ||||||||
Remarks | ||||||||
Report date | Oct 18,2023 | Issue date | 年 月 日 |
2. Raw material chemical properties
Raw material | Clay | Raw material source | ||||
Entrusted party | Submit date | 8-Oct-23 | ||||
Submit party | Analysis | Chemical component | ||||
Analysis result(%) | ||||||
Item | Clay | |||||
SiO2 | 57.81 | |||||
Al2O3 | 11.35 | |||||
Fe2O3 | 4.64 | |||||
CaO | 8.73 | |||||
MgO | 2.52 | |||||
K2O | 2.8 | |||||
Na2O | 1.78 | |||||
SO3 | 0.44 | |||||
TiO2 | 0.65 | |||||
Loss on ignition | 8.76 | |||||
Remark | ||||||
Report date | 18-Oct-23 | Issue date |
3. Drying properties
The shaped samples are dried naturally for 24 hours and then put into the oven at 105±5℃ for 8 hours. There were no cracks on the dried brick samples, and the strength is quite good, and drying line shrinkage ratio is 1.76%.
4. Firing properties
(1) Temperature gradient furnace: small samples (40x20x10mm) is fired in the temperature gradient furnace to measure the firing temperature and temperature range. Firing conditions is as follow:
Heating rate: <200℃/hr
Firing cycle: 6 hours
Heat preservation: 30 minutes
Cooling method: cooled to room temperature together with the furnace
Figure 1 Small-sized sintered bricks burned in temperature gradient furnace from 900℃~1150℃
(2) Product firing shrinkage rate and water absorption rate: firing shrinkage rate and water absorption rate are measured on the samples fired in the gradient furnace, and the relationship curves among temperature, water absorption and shrinkage are shown in Fig. 2.
The sample firing system is listed below (table 1) by combing figure 2 (firing curve) and sample firing condition at different temperature.
Table 1 Sample firing system
Raw material | Firing temperature range | Firing temperature |
Clay sample | 980~1080℃ | 1030℃ |
(3) High temperature firing furnace: the dried samples were fired in the high temperature furnace according to the regular firing system. Firing conditions were as follow:
Room temperature~firing temperature 150℃/hr
Firing temperature 1 hour insulation
Cooled to room temperature together with the furnace
Clay samples: small-scale experimental sintered brick sample fired at 1040℃
The firing temperature for clay sample is determined at 1040℃. After firing, the sample color turns into light yellow, with a clear sound upon tapping. The sample shrinkage ratio while firing is 0.24%.
5. Lime bursting test
The test was carried out on fired samples, and there was no lime bursting phenomenon occurred in the small-scale simulated test.
6. Frosting test
The test was carried out on fired samples, and there was no frosting phenomenon occurred in the small-scale simulated test.
7. Conclusion and suggestion
(1) Sample clay has higher content of CaO, low plasticity and low drying sensitivity.
(2) When performing small-scale sintered bricks simulated test with 100% clay as raw material, the shaping process is rather difficult, the wet green brick strength is poor, which need to remind the client. The drying and firing performance of the shaped samples are good with moderate burning temperature from 980℃~1080℃.
(3) No lime bursting phenomenon occurred when proceeding small-scale simulated test.
(4) No frosting phenomenon occurred when proceeding small-scale simulated test.